BUILDING THE BEST WHEELS
Skip To: Building to Maximize Stiffness | Do Carbon Wheels Lack Vertical Compliance?
The more you learn about wheel building, the more you learn that building a good wheel is a difficult series of compromises between the rim, the number of spokes, the type of spokes, the spoke lacing cross pattern, the spoke orientation and the spoke tension. Here we explain our logic for why we build wheels the way we do. You will find that other builders may recommend something different. Keep in mind, there is no ideal or perfect way to build wheels, it’s always about compromises and building the right wheel for you and your riding style. If you don’t agree with what we do, we understand, and that’s why we’ll sell you a rim so you can build it however you want 🙂
Our wheels are built to optimize lateral stiffness. We feel that lateral stiffness is the most important factor to how a wheel feels on the trail; wheels with high lateral stiffness don’t have that “floppy” feel in slow rocky turns and they give the bike that “on-rails” feeling around a banked corner. Our wheel building philosophy is based around maximizing lateral stiffness. The larger the diameter of the wheel, the more important (and difficult) it becomes to maximize lateral stiffness. When people say a wheel “feels flexy” they are describing low lateral stiffness, and we’ve ridden plenty of flexy 29 inch alloy wheels ourselves. Making stiffer wheels is really the reason we started making carbon mountain rims in the first place, so it follows that we build our wheels to further maximize lateral stiffness.
First, a few definitions:
Lateral Stiffness: The wheels resistance to deformation along the axis parallel to the hub axle.
Radial Stiffness: The wheels resistance to deformation inward or outward radially from the center of the wheel.
Tangential Stiffness: The wheels resistance to deformation from acceleration or braking forces imparted near the hub.
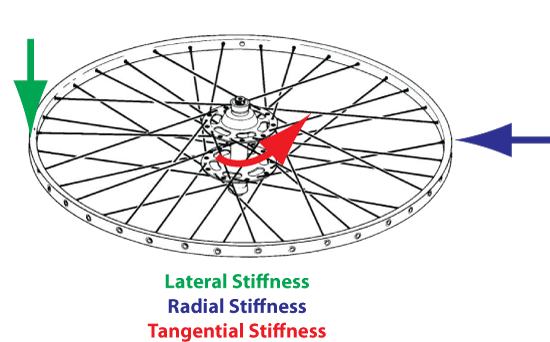
Increasing Stiffness
Our goal is to maximize lateral stiffness, so how do you this? Well, in order of importance the contributing factors to lateral stiffness are*:
- The rim stiffness
- The number of spokes
- The spoke bracing angle
- The gauge of the spokes
- The lacing pattern
Clearly the rim is the first place to attack the stiffness problem, and we’ve done that. Our wide carbon rims are orders of magnitude stiffer than an equal weight aluminum rim. So let’s move on to the other wheel parameters.
Number of Spokes
As we said above, number of spokes is the 2nd most important factor when building a set of stiff wheels. Therefore, we use 28-32 spokes by default for mountain rims and 24-28 for road disc rims. It may not be “trendy,” or “look cool” but it’s the right thing to do from an engineering standpoint. Many people assume that with super-stiff carbon rims you can “get away” with very few spokes. Perhaps you can depending on what level of stiffness you are happy with, but there is more to the story, and that’s opposite load deflection. Read on..
You may have assumed that when wheels rub against the chainstay, fork or cantilever brakes, it is a symptom of flexy wheels. In reality, the situation is more complicated than that. This is because lateral stiffness is affected by two major parts of the wheel; the rim stiffness and the spoke system stiffness. Our carbon rims provide a very high level of rim stiffness, so much so that they can literally overpower low spoke stiffness and this can actually amplify lateral deflection at parts of the rim away from the lateral loading point (the ground). In other words, with all other things equal, carbon rims can increase the rubbing against your chainstays, fork or cantilever brakes! It’s a bit counter-intuitive, but this effect is due to our carbon wheels not conforming or bending when subjected to lateral loads, so the effects of low spoke stiffness are actually amplified by the stiffness of the rims. In contrast, a lightweight aluminum rim conforms as lateral loads are applied, and this deformation masks the chainstay rubbing effect (but it also makes your steering feel sloppy and robs you power!). So why are low spoke count wheels so popular? Like we said before, it’s usually due to the desire for wheels to “look cool” or to be uber light weight because a marketing department decides this would sell more wheels. Far too many manufacturers don’t understand the physics behind what is really happening and they use too few spokes on their carbon wheels, making them have far too much opposite load deflection. Our goal is to build the best performing wheels, and to do that we have made a careful choice between rotational weight and spoke stiffness such that the wheel system as a whole is optimized.
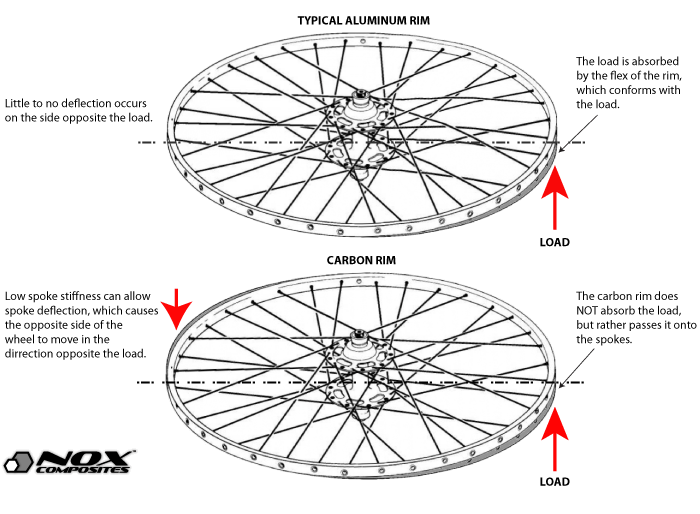
Our most popular custom mountain wheels use 32 Sapim CX-Ray spokes, which is an ideal combination of low weight and high enough spoke stiffness for most riders to minimize lateral deflection. If you weigh more than 200 lbs, are a powerful rider on a single speed, or a very aggressive rider, you might want to consider a thicker gauge spoke, but since spoke gauge is number 4 on our list it isn’t something we recommend for most riders. Feel free to contact us to discuss a custom build spec.
Lacing Cross Pattern
Besides the factors already mentioned, the last important contributor is the lacing pattern. Let’s ignore spokes for a minute (we’ll come back to that) and deal with lacing patterns first. In short, 2-cross lacing provides the best lateral stiffness compared to 3-cross or 4-cross. To learn more about this, we recommend reading this paper by Duke University Professor Henri Gavin. Lack of lateral stiffness is not as much of a problem with smaller diameter wheels, which is why 3-cross has been so popular with 26 inch wheels. Using 3 or even 4-cross lacing does reduce the radial stiffness of the wheel, and some people claim this can provide a more vertically compliant ride, however our research and calculations (see below) show that the effects are so small that no rider could discern them, hence we recommend 2-cross for most riders.
Spoke Type
Remember spoke gauge was number 4 of 5 on our list above of stiffness factors. What does this mean? Well, it means that spoke gauge isn’t all that important when you are trying to maximize wheel stiffness and therefore it’s a great place to save some weight. Of course, the trade off is that lightweight spokes are less durable. If you are looking for a lightweight/high-performance wheelset, then we recommend bladed spokes like the Sapim CX-Ray. The reasons for this is that they go through an additional forging processing which increase the fatigue life of the spoke. It’s also easier and more precise to build with a lightweight bladed spoke because we can use a special tool to hold the spoke as we tighten the nipple, thereby eliminating spoke “wind-up” which happens when you build with thin gauge butted spokes. We acknowledge that there is much debate about spoke strength, fatigue life, why spokes break, etc. In the end, our own anecdotal evidence agrees with the spoke manufactures claim that lightweight bladed spokes are more durable than an equivalent weight round butted spoke. For these reasons, we generally recommend bladed spokes to most customers. With that said, riders more than 200lbs, or those riders wiling to sacrifice weight for durability would be better served with a larger cross-section spoke like Sapim Race, Force or D-Light. Cost can be a factor too of course as bladed spokes tend to be approximately three times the cost of round spokes.
Spoke Orientation
Ok, here is where things can get even more complicated, but we will try to keep it simple. In a nutshell, we orient our spokes so that the front is optimized for braking forces and the rear is optimized for acceleration forces. When you apply force to the pedals, you are tensioning the rear wheel’s trailing spokes and compressing the rear wheel’s leading spokes. We build the rear wheels to have the spokes under tension (the trailing ones) with their elbows out. Spokes with the elbows out are more durable and able to withstand more stress because they are wider (they are on the outside of the hub) and they have the additional support of the hub flange. In the front the situation is the opposite, the most significant force is from braking. Therefore the leading spokes in the front are placed elbows out.
Spoke Tension
There is a lot of misconception out there about high-tension wheel builds and how it relates to lateral stiffness. Many people assume that higher tension provides higher lateral stiffness, however this isn’t true. Taking a wheel system and changing nothing else but spoke tension will not improve lateral stiffness (see Daman Rinard’s Wheel Stiffness Test for more info). However, using an asymmetric rim will increase both net tension AND change the bracing angles. This can confuse people, because they see the net increase in spoke tension and assume the tension was responsible for the increase in lateral stiffness. In reality, the improvement in stiffness is due to the equalization of bracing angles between the drive side (DS) and non-drive side (NDS). Let’s look at an example with a Chris King hub. Using a normal symmetric rim on a 29er, the bracing angles will be 4.4 deg on the DS and 7.4 deg on the NDS. By keeping all else the same except for using one of our asymmetric rims with a 2.6mm offset, the angles change to 4.9 deg on the DS and 6.8 deg on the NDS. If we run the numbers we see a gain in lateral stiffness on the DS by (4.9/4.4)^2 = 24% and a loss of lateral stiffness on the NDS by (6.8/7.4)^2 = 16%, but overall there is a net GAIN of 8%. To help visualize this, check out this illustration. The point to take away is that with all else equal, you will see a higher net tension with our asymmetric rim which is a great thing for wheel strength and durability and you’ll also see an increase in lateral stiffness (assuming it is a dished wheel of course, which all disc brake wheels are). But, going to higher and higher tension in search of stiffness doesn’t work, it just adds unnecessary strain on your spokes, nipples, hubs and rims. About 120 kgf is the sweet spot to be high enough to prevent spokes coming loose and have no issue with loss of strength due to certain spokes losing tension during riding/landing jumps, etc..
Vertical Compliance and Carbon Rims
Let’s talk a bit about vertical compliance. We often get questions like “are carbon wheels too harsh?” or “I heard carbon wheels make the bike really uncomfortable, is that true?” The short answer is no, you will not be able to tell any difference in vertical compliance between a carbon wheel and an aluminum wheel. In short, changes in vertical compliance between two wheel setups can be contributed to other factors like tire volume, tire casing, tire pressure, frame flex, handlebar flex etc., not the wheel setups. No spoked bicycle wheel, even super-light alloy wheels with thin gauge spokes, have enough vertical compliance for you to feel a difference. If you are interested in proof of this, keep reading.
First, let’s be clear that in terms of vertical compliance we are talking about displacement due to low radial stiffness. Stiffness (k) is defined below, where F = force (mass x acceleration) and δ = displacement. So given the same radial forces, for a rim to have a “high” level of vertical compliance (displacement) it would need to have low radial stiffness.
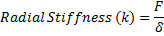
From Gavin’s elastic frame analysis*, it has been shown that for a typical bicycle wheel, the radial stiffness (k) is on the order of 2500-4500 N/mm depending on the spoke gauge, lacing pattern, the elastic modulus of the rim and moment of inertia of the rim. Gavin’s work was based on typical aluminum rims, so he used a value of 69 GPa for the elastic modulus and he analyzed over a range of bending moments of inertia from 500-1500mm^4. Carbon fiber has a higher elastic modulus, about 181 GPa. The rim’s bending moment of inertia depends of the thickness of material and shape of the rim, which will be close between the two materials, so let’s just keep it simple and assume that the bending moment of inertia is the same between a given aluminum rim and carbon rim.
So the point of all this is to compare vertical compliance between an aluminum rim and a carbon rim, so let’s run some numbers and see what we get. Let’s first assume a 165lb rider on a 30lb bike, so about 90kg. Let’s also assume that the weight is distributed 60/40 between the two wheels, so we’ll say 54kg of mass is loading the rear wheel. And the final assumption is that we’re using the same 1.8mm spokes with both wheels. So, from Gavin’s* paper (Figure 5) we see stiffness values of about 3500 N/mm for an aluminum rim with a middle of the road bending moment of inertia (1000mm^4). So just sitting on the bike, with the acceleration of the wheel due only to gravity, (1G or 9.8 m/s^2), we get:
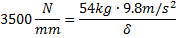

So obviously there is VERY little vertical displacement at only 6 thousandths of an inch! But let’s make things more complicated and say you are ripping along a trail and hitting some 2” roots at high speed. This seems to be a typical scenario people describe when they say they feel a wheel has low vertical compliance. A 2” root hit at 15mph would introduce about ~3Gs into the wheel system (based on an a simplified calculation, an accelerometer mounted on the wheel would be ideal to get real-world numbers, but this is close). So running the numbers again for 3Gs of acceleration we get:
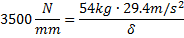

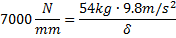

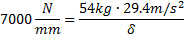

Rim Type |
Acceleration (165lb rider) |
Vertical Deflection |
Aluminum |
Static Deflection (1G) |
0.006 inches |
Aluminum |
High Speed Impact (3Gs) |
0.018 inches |
Carbon |
Static Deflection (1G) |
0.003 inches |
Carbon |
High Speed Impact (3Gs) |
0.009 inches |
From the table above, you can see that the difference in deflection between an aluminum rim and a carbon rim is (at maximum) 0.009 inches. That’s about the thickness of 9 human hairs! In short, it’s just not possible for a rider to discern that small of a change. So why do people swear they feel these differences?
Let’s consider the vertical compliance due to your tires. A typical 29×2.25” tire is about 50mm tall. Even if we leave all the calculations aside (which are surprisingly complicated), most of us run pressures off-road of about 20-30psi, which generally results in ~20% tire drop (0.39 inches) when you are sitting on the bike. With correct tire pressure for your weight, a direct impact with a 2” diameter log at 15 mph will result in a ~50% (0.98 inches) collapse of the tire casing as it absorbs the impact. So the tire deformation provides more than 100 TIMES the vertical compliance than that of the wheel, whether it is aluminum or carbon. It should be clear now that not only can no rider can discern the difference in vertical compliance between any two wheels, but rather these perceived differences must be coming from changes in tire volume, air pressure changes (even a few psi makes a big difference), tire casing, or even frame/fork/stem/handlebar flex. If you are hesitant about going with a carbon mountain wheel because you’ve heard or read about harshness, or even seem some carbon rims on the market which claim to be more vertically compliant than others – we suggest you take your focus away from the rim material and look at rim width! Going to a wider rim not only lowers rolling resistance, it increases the volume of the tire, so if you are coming from a more traditional narrow rim to our wider carbon rims, not only should you not be worried about less vertical compliance or comport, you should actually expect an increase in vertical compliance (comfort) due to higher tire volume!
*References:
Brandt, Jobst. The Bicycle Wheel, Avocet, 1993.
Rinard, Damon. Damon Rinard’s Wheel Stiffness Test, url: http://sheldonbrown.com/rinard/wheel/index.htm, last accessed 09/2013.
Gavin, Henri, Bicycle Wheel Spoke Patterns and Spoke Fatigue, url: http://people.duke.edu/~hpgavin/papers/HPGavin-Wheel-Paper.pdf. last accessed 09/2013