TECHNOLOGY
COMPOSITE RIM DESIGN AND CONSTRUCTION
Each of our rims are custom designed with specific composites and layups to make the strongest and lightest rims available for the intended application. We don’t use any “open mold” rims. We control the entire process from CAD modeling through mold development, layup, prototyping, testing, production, finishing, QC and decal application. Our rims are made with what we consider the optimum blend of high strength and high modulus carbon fiber sourced directly from Toray in Japan. Carbon fiber’s main specifications are tensile strength and tensile modulus. Composites engineers have to make careful trade-offs between high tensile strength (the force required to break) and high tensile modulus (the stiffness or force required to cause non-permanent deflection) materials. In other words, if you use only high-modulus (extremely stiff) fiber, then the rim becomes brittle and would easily crack from a rim strike. At the other extreme, if you used only high-strength fiber, then the rim would be flexy. Of course, material selection is important, but it’s just one facet of a good design. The best rim designs result from using the correct materials, ideal layup patterns, appropriate use of both unidirectional and weaved fabrics, ideal material thickness and good production techniques. These design tradeoffs are apparent when you examine any good carbon rim, and you’ll spot them when you first pick up a Nox rim.
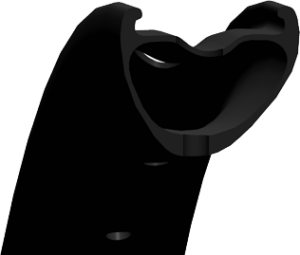
UniWeave Construction
Our unique carbon layup, called UniWeave, makes use of two different carbon fiber fabric types “stacked” to improve the strength, improve stiffness, lower costs and maximize durability. 3K tow woven fabric is used to provide strength in areas where the rims are drilled (spoke holes, valve holes and nipple access holes). Unidirectional fiber layups provide the core rim strength. This unique construction method dramatically improves the strength and durability of the rim while providing the highest stiffness to weight ratio possible.
RockGuard Hookless Rim Protection
The one downside to composite rims used to be they could not withstand rock direct rock strikes due to the relative brittleness of the material compared to aluminum. We’ve solved this issue with the RockGuard HL bead hook, our next generation of bead hook protection from rocks, roots or road hazards. Core to this design is the optimization of the carbon layup such that the final unidirectional weave layers are never broken near the bead. This seamless layer of fiber prevents delamination and makes the bead as strong as possible. Combine this incredibly strong layup with our industry leading extra-thick bead width and tapered bead hook shape and you’ll see why this is the strongest carbon rim on the market.
Please note that the hookless rim designs are only suitable for low pressure (< 45 psi) applications.
RockGuard Rim Protection
The RockGuard bead hook protection system is used on rims designed for more than 45psi. The system is designed to improve the rim’s strength and resistance to cracking when you directly hit a rock, root, curb, or other road debris. It’s a combination of extra material thickness and ideal surface fiber orientations to provide the maximum impact resistance. In the event of a hard rim strike (say your air pressure was way too low) the RockGuard rim bead is not only more resistant to surface damage, but our lay-up minimizes the chance of delamination which keeps the crack from propagating and ensures that the rim/wheel maintains integrity so you can ride out.
Anti-Burp Bump
Our rims feature a slight bump between the drop channel and the outer bead seat. This Anti-Burp Bump serves two purposes. First, it helps you install a tubeless tire by increasing the bead diameter just outside the drop channel so the tire forms an air-tight seal easily and the air pressure is able to push it out into the bead seat. Secondly, once a tire is seated, the bump resists inward motion of the tire bead, making it less likely that the tire will “burp” air during botched landings low-pressure riding.
WHAT ELSE MAKES OUR RIMS UNIQUE?
Stiffness
Of all the components that make up a bicycle wheel, the stiffness of the rim makes the largest contribution to overall stiffness. There is a lot of talk out there about bracing angles, hub flange width, hub flange diameter, spoke gauges etc., but all those factors contribute very little compared to the stiffness qualities of the rim you are building with. Stiff wheels improve tracking and maximize power transfer, both of which will make your riding faster and more fun. Our composite rims are exceptionally stiff! Compare them side by side to alloy rims of the same weight, and you’ll be blown away with the difference. Our in-house built wheelsets are built to further optimize lateral stiffness; you can read more about how we build our wheels Wheel Building Theory
Width
Wider rims are better, as shown by both scientific and anecdotal evidence. Wider rims increase the volume of the tire, allowing you to run lower pressure and obtain more grip with lower rolling resistance. Another beneficial side effect is that wide rims are much less susceptible to “burping” when run tubeless. The traditional negative is that wider rims are heavier. Nox rims solve that problem by using composite materials which allow us to design wide rims at the same or less weight than narrow alloy rims.
Asymmetrical
Asymmetrical rims build up into stiffer, stronger and more reliable wheels by improving the bracing angles of a dished wheel and equalizing the spoke tensions between the drive and non-drive side spokes. On a mountain bike wheelset with disc brakes, both the front and rear wheels have significant dish. With traditional rims, the rim is centered (or dished) by decreasing spoke tension on one side relative to the other so that the rim is pulled into center. A typical symmetric-rimmed mountain bike rear wheel requires spoke tension ~40% less on the non-drive side. This mismatch in spoke tension means the wheels is weaker than it could be, the lateral stiffness could be improved, and the low-tension spokes are prone to coming loose over time. Asymmetrical rims help fix these issues by offsetting the nipple holes so that the bracing angles are improved and the spoke tension between the drive and non-drive side is more equalized. Our rims have 2.4-2.6mm of offset which we’ve found is the sweet spot; improving spoke tension balance by about 15% but also allowing you to use the same rim for either the front or rear by simply flipping the rim around. The correct position is indicated on each rim. For a better visualization of how asymmetrical rims help build stronger and stiffer wheels, check out the drawing to the left.
Light
Nox was founded by racers who know firsthand that a light wheelset is one of the few bike upgrades that can actually make you faster and help you ride longer. Rotational weight is important to minimize if you want the most performance, so we keep our rim weights as low as possible. However, don’t expect to see crazy light rims from us; while weight is important, we also design our wheels to be stiff, strong, durable and safe.
Durability
Carbon rims/wheels are a large investment, and one we think should make sense from a durability standpoint. Our rims are designed to be durable and last for years of hard riding and racing. These rims are light and fast enough for race day, yet durable enough to train on daily. It’s also important to realize that you’ll be riding a wheel, not just a rim, so many aspect of our rims are designing for maximum wheel build durability. The most important aspect of keeping a wheel true is even and high tension. Our rims are safe to build to higher tensions than equivalent weight alloy rims, and a higher tension wheel will be more durable over the long haul. High tension spokes (recommended 120 kgf) are less likely to come loose and less likely to break (keep in mind, there is an upper limit here! If you go above 120 kgf you will start to put too much strain on the nipple/hubs/spokes and that can lead to premature failure). How do we get away with such high tension? We use a proprietary manufacturing process that allows us to precisely control the material thickness in the nipple bed. Precise nipple bed thickness control combined with our UniWeave construction creates some seriously strong nipple seats. We’ve tested for spoke pull-through strength, and we can tell you that it’s somewhere north of 880 Lbf. The spokes always break first before we get to higher loads! To put that in perspective, 3 spokes and 3 spoke holes could support the weight of a small car!
Tubeless Ready
There is little reason to run tubes on a mountain bike anymore. Tubeless provides better traction, no pinch flats, lower rolling resistance, more comfort, etc. We know that most customers running our rims will be doing so tubeless, so we go through great pains to ensure that our rims will work perfectly when set up tubeless. We also design them to make setting up tubeless tires as easy as possible. Features like our Anti-Burp Bump increase the bead seat diameter just outside the channel so tires are easier to initially inflate. This same feature also locks in the bead to ensure burp-free performance. Of course, our rims also perform just fine if you choose to run tubes.